BDO technology
Benefits
Robust and efficient process from low-cost acetylene
Low capital cost due to highly active catalyst
Low-cost catalyst
High-purity process
Low OPEX
Over 40 years of operating experience and technology improvement
How It Works
The chemistry to manufacture BDO from acetylene and formaldehyde is well-established and comprises two primary steps.
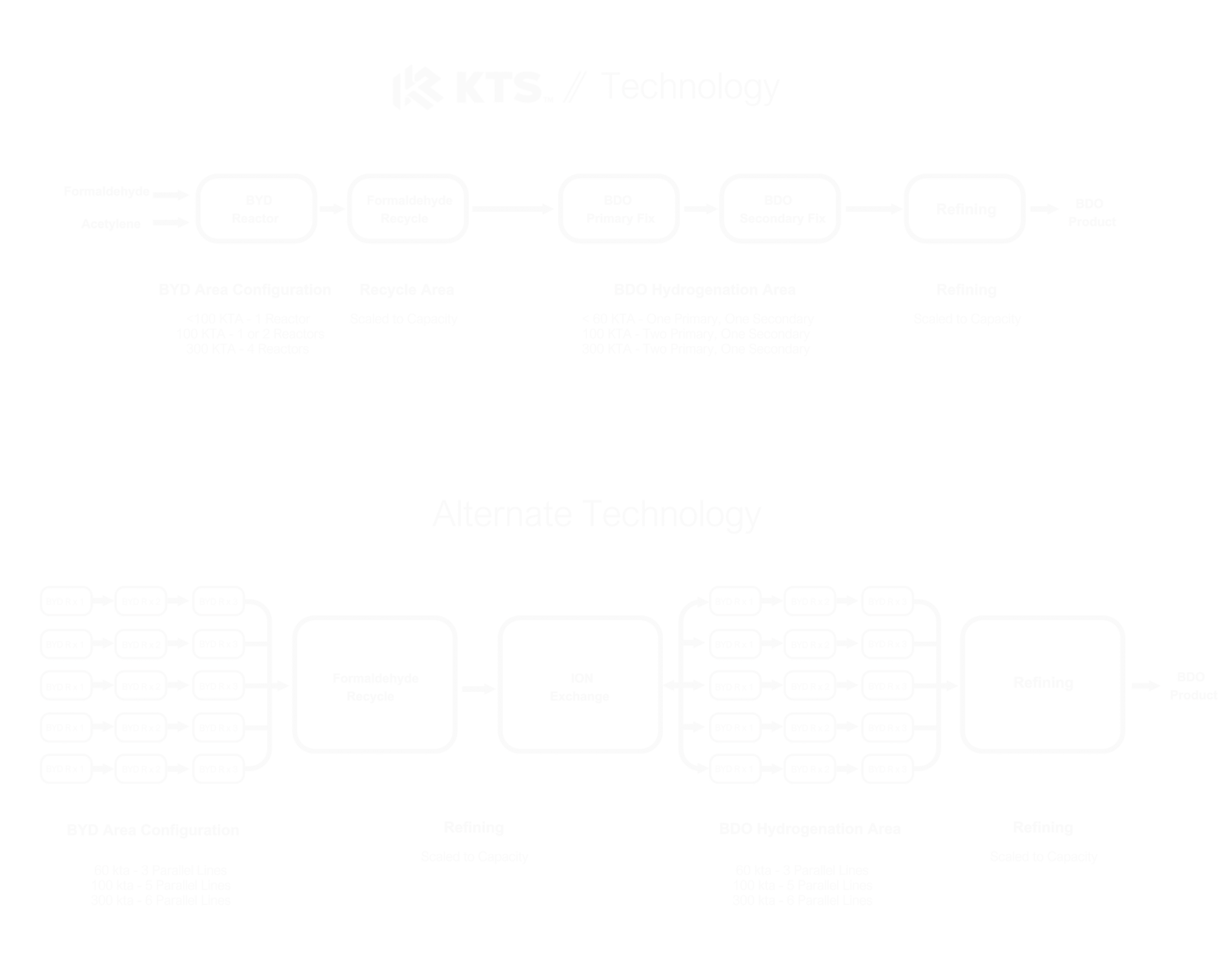
While the chemistry is straightforward, the reactants must be handled with care and the process must be designed to ensure safe operation. The KTS process utilizes a highly active catalyst in Step 1 that allows us to design a one or two reactor for a 100 kta BDO plant. Other processes are configured with three reactors in series for each line and five parallel lines.
Our Step 2 hydrogenation reactors are designed for high-pressure hydrogenation to ensure the highest yield to BDO and minimum color forming unsaturated in the final product. Other available technologies utilize low and medium pressure hydrogenation reactors, and the story is similar to Step 1.
At 100 kta scale, we utilize two primary reactors and one secondary reactor. The other available technology employs three reactors per line and five lines in parallel. In total, a KTS BDO plant at 100 kta is designed for either four or five total reactors whereas the other available technology requires 30 reactors. At 300 kta scale, our design requires only seven reactors compared to 48 for the next best alternative.
Our Proven Offer
KTS’ base technology offering includes a Process and Basic Design Package (PBDP), technical services to support detailed design, procurement, commissioning and start-up, training and on-going post-acceptance technical services.
In addition, we can leverage the capabilities across Koch Engineered Solutions to customize our offer and include equipment supply, project management service and other project execution options to meet our license needs.
Ready to learn more about our efficient technology?
Learn about our latest advancements and capabilities.